Research Project
Additive Manufacturing of Aerospace Heat Exchanger
(Consortium for High-volume Additive Manufacturing of Aerospace Heat Exchanger and Talent Development)
Lead Researchers
- Prof. Bingbing Li, Department of Manufacturing Systems Engineering and Management*
- Prof. Christoph Schaal, Department of Mechanical Engineering*
Collaborators
- NASA JPL:
- Dr. Ryan Watkins*
- Dr. Douglas Hoffman
- Dr. Richard Otis
- Dr. Bryan McEnerney
- NASA Goddard:
- Mr. Ryan McClelland*
- UCLA:
- Prof. Xiaochun Li
- Prof. Morris Wang
- Honeywell:
- Mr. Gregory Colvin*
- Rafael, Maldonado Comas*
- Campos, Natalie*
- Bob DeMers
- Castheon Inc.:
- Dr. Youping Gao*
- Mr. Steve James
- ASTM Additive Manufacturing Center of Excellence (AM CoE):
- Mr. Shane Collins*
- SimInsights Inc.:
- Mr. Rajesh Jha*
- El Camino College:
- Mr. Jose Anaya*
- External Advisory Committee:
- Mrs. Marilee J. Wheaton (The Aerospace Corporation)*
- Mr. Dale Turner, DOE CESMII*
Student Team
- Changyu Ma, PostDoc Material Science and Engineering*
- Jianhao Zhu, MS Manufacturing Systems Engineering*
- Marshall Doyle, MS Mechanical Engineering*
- Zachary Liu, student at Sierra Canyon School*
- Donald Palomino, Fellow, M.S. candidate in Manufacturing Systems Engineering at CSUN
- Paula Logozzo, Fellow, undergraduate student in Mechanical Engineering at CSUN
- Elliot Sadler, Fellow, M.S. candidate in Manufacturing Systems Engineering at CSUN
- Bodia Borijin, Intern, B.S. candidate in Structural Engineering at UCSD
- Andrew Wang, Intern, Portola High School
Funding
- Funding Organization: NASA
- Funding Program: MUREP Aerospace High-Volume Manufacturing and Supply Chain Management (MUREP High Volume), Grant number: 80NSSC22M0132
Note: names marked with an asterisk (*) indicate current team
Abstract
SYNOPSIS
- Crack-free HAYNES® 282®, a superalloy developed for high temperature structural applications, was fabricated using the Renishaw AM400 machine with optimized parameters. The reduction of porosity in as-printed alloys is related to laser parameters, including laser speed, hatch distance, and other factors.
- The typical structure of L-PBF-fabricated HAYNES® 282® consists of columnar structures, equiaxed grains, and ultrafine grains. Processing parameters play a crucial role in the precipitation of the strengthening phase, with spherical and cubic strengthening phases observed in alloys printed using chessboard and meander patterns, respectively.
- L-PBF-fabricated HAYNES® 282® exhibited excellent mechanical properties in both as-printed and heat-treated states, with high yield strength and ultimate tensile strength (UTS).
Heat exchangers are widely utilized in engine, avionics, and environmental control systems of aircrafts, as they help to control heat and maintain temperature by removing excess heat from the systems. While heat exchangers for military and commercial applications, such as the three most recent commercial transport bleed air system precoolers—A350, B737MAX, B777X, are almost always life-limited by thermal fatigue—caused by continual rapid temperature transients due to aircraft takeoff, landing, and other operations. Enhanced alloys and generative design used for additive manufacturing is expected to improve performance and speed and agility in the design and development process of heat exchangers. Implementation of AM could significantly improve the supply chain efficiency, rendering it a worthwhile investment for global supply chain. AM helps to balance inventory levels and increase responsiveness while decreasing disruptions and carbon emissions in the supply networks. One present limitation for aerospace heat exchangers is that the minimum viable material thicknesses are considerably greater than state-of-the-art, resulting in unacceptable weight increases. One mitigating factor is that the relatively thick walls that will be required for the high-temperature, high-pressure modular power system heat exchangers may be within AM capability. AM heat exchangers will provide the following benefits of AM heat exchanger design and fabrication: fabricate multi-piece assemblies as one part (no joining techniques required), greatly reduced lead times, greatly reduced part count, potential for conformal shapes or design features that are not currently practical, automate the build process (less rework), and reduce weight.
High-temperature aerospace heat exchangers, for military and commercial applications, are almost always life-limited by thermal fatigue—caused by continual rapid temperature transients due to aircraft takeoff, landing, and other operations. Metal Additive manufacturing (AM) is reshaping the production and supply chain eco-system with its diverse printable materials to increase speed and agility in the design and development process. Implementation of AM could significantly improve the supply chain efficiency, rendering it a worthwhile investment for global supply chain. AM helps to balance inventory levels and increase responsiveness while decreasing disruptions and carbon emissions in the supply networks. One present limitation for aerospace heat exchangers is that the minimum viable material thicknesses are considerably greater than state-of-the-art, resulting in unacceptable weight increases. One mitigating factor is that the relatively thick walls that will be required for the high-temperature, high-pressure modular power system heat exchangers may be within AM capability. AM heat exchangers will provide the following benefits of AM heat exchanger design and fabrication: fabricate multi-piece assemblies as one part (no joining techniques required), greatly reduced leadtimes, greatly reduced part count, potential for conformal shapes or design features that are not currently practical, automate the build process (less rework), and reduce weight.
Lead Researchers
- Prof. Bingbing Li, Department of Manufacturing Systems Engineering and Management
- Prof. Christoph Schaal, Department of Mechanical Engineering
Collaborators
- NASA JPL: Dr. Douglas Hoffman, Dr. Richard Otis, Dr. Ryan Watkins, Dr. Bryan McEnerney
- NASA Goddard Space Flight Center: Ryan McClelland at Instrument Systems and Technology
- UCLA: Dr. Xiaochun Li, Dr. Morris Wang
- Honeywell Aerospace: Gregory Colvin, Bob DeMers
- Castheon Inc: Dr. Youping Gao, Mr. Steve James
- ASTM Additive Manufacturing Center of Excellence (AM CoE): Mr. Shane Collins
- SimInsights Inc: Mr. Rajesh Jha
- El Camino College: Mr. Jose Anaya
Student Team
- Dr. Changyu Ma, Postdoc in ARCS at CSUN
- Donald Palomino, Fellow, M.S. candidate in Manufacturing Systems Engineering at CSUN
- Paula Logozzo, Fellow, undergraduate student in Mechanical Engineering at CSUN
- Elliot Sadler, Fellow, M.S. candidate in Manufacturing Systems Engineering at CSUN
- Bodia Borijin, Intern, B.S. candidate in Structural Engineering at UCSD
- Andrew Wang, Intern, Portola High School
Funding
- Funding Organization: NASA
- Funding Program: MUREP Aerospace High-Volume Manufacturing and Supply Chain Management (MUREP High Volume), Grant number: 80NSSC22M0132
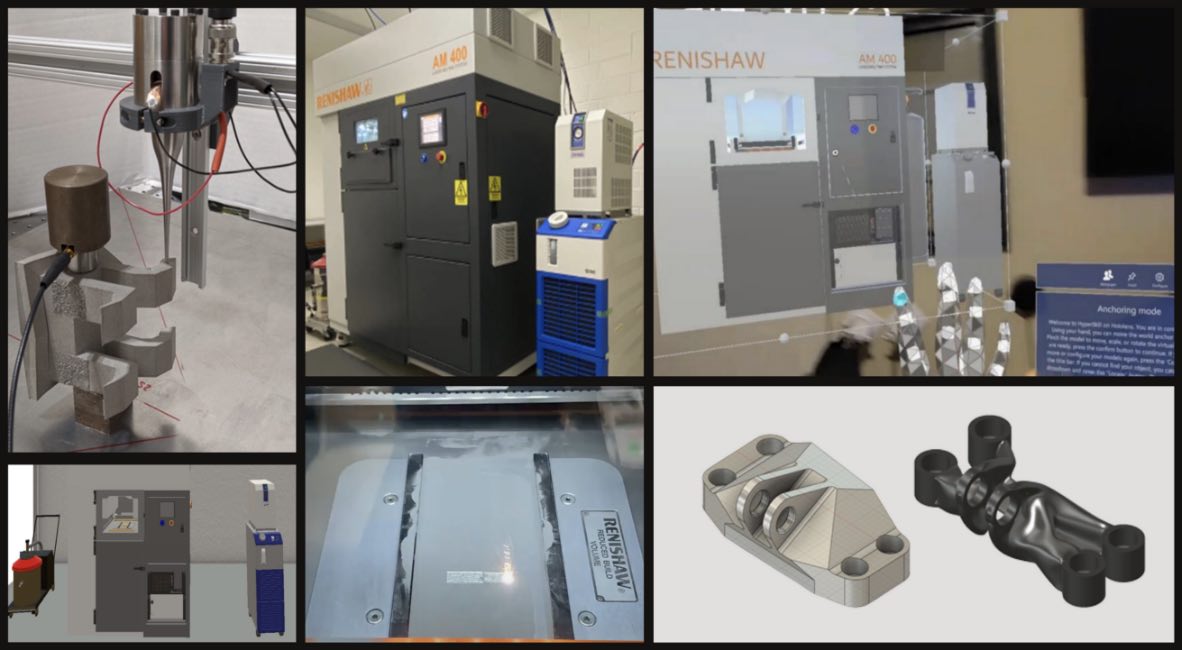
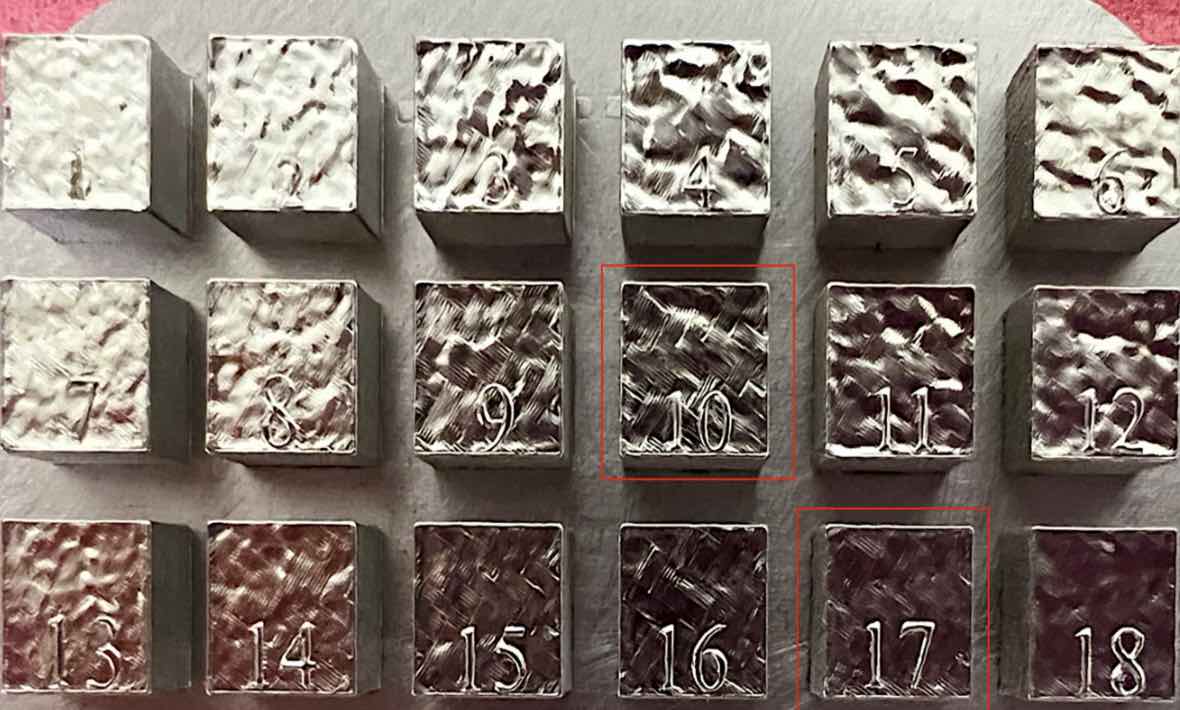
Research Objectives
-
The Autonomy Research Center for STEAHM (ARCS), in partnership with NASA JPL, academia and private industry partners, will create a Consortium for High-Volume Additive Manufacturing of Aerospace Heat Exchanger and Talent Development.
-
The project will leverage ARCS’s unique student talent and its access to JPL personnel and facilities, plus its strong partners, to conduct convergence.
Research Methods
-
Develop robust superalloys by nanoparticles self- dispersion to improve the performance of heat exchanger
-
Identify best practices of the generative design for additive manufacturing (AM)
-
Cut the sample, observe it with micro CT, detect the roughness after corrosion precipitation, and finally summarize it through Transmission Electron Microscopy (TEM) for fusion in Laser Powder Bed Fusion (LPBF) additive manufacturing
Research Deliverables and Products
-
Cracks-free HAYNES® 282® was successfully fabricated with chess board printing patterns, and combination of optimized hatch distance and VED was selected to achieve low porosity and smooth surface in as-printed HAYNES® 282®.
-
Sub-grain was observed in as-printed HAYNES® with fine γ′ phase, equiaxed and elongated grain were observed in X-Y and Y-Z planes of heat treated specimen, respectively. The 2- step aging heat treatment contributes to finer γ′ phase and precipitation of carbides along grain boundaries.
-
In as-printed status, specimen has higher yield stress (YS) and ultimate tensile stress (UTS) in the X-Y plane, while higher engineering strain of 43.8% was observed in Y-Z plane.
Commercialization and/or Societal Impact Opportunities
-
Application: High-performance materials
-
Key Values: Improved mechanical properties, reduced porosity and crack-free components
-
Potential Customer: Aerospace industry
Research Timeline
Start Date: 5/16/2022
End Date: 5/15/2025
3 year project
Lead Researchers
- Prof. Bingbing Li, Department of Manufacturing Systems Engineering and Management*
- Prof. Christoph Schaal, Department of Mechanical Engineering*
Collaborators
- NASA JPL:
- Dr. Ryan Watkins*
- Dr. Douglas Hoffman
- Dr. Richard Otis
- Dr. Bryan McEnerney
- NASA Goddard:
- Mr. Ryan McClelland*
- UCLA:
- Prof. Xiaochun Li
- Prof. Morris Wang
- Honeywell:
- Mr. Gregory Colvin*
- Rafael, Maldonado Comas*
- Campos, Natalie*
- Bob DeMers
- Castheon Inc.:
- Dr. Youping Gao*
- Mr. Steve James
- ASTM Additive Manufacturing Center of Excellence (AM CoE):
- Mr. Shane Collins*
- SimInsights Inc.:
- Mr. Rajesh Jha*
- El Camino College:
- Mr. Jose Anaya*
- External Advisory Committee:
- Mrs. Marilee J. Wheaton (The Aerospace Corporation)*
- Mr. Dale Turner, DOE CESMII*
Student Team
- Changyu Ma, PostDoc Material Science and Engineering*
- Jianhao Zhu, MS Manufacturing Systems Engineering*
- Marshall Doyle, MS Mechanical Engineering*
- Zachary Liu, student at Sierra Canyon School*
- Donald Palomino, Fellow, M.S. candidate in Manufacturing Systems Engineering at CSUN
- Paula Logozzo, Fellow, undergraduate student in Mechanical Engineering at CSUN
- Elliot Sadler, Fellow, M.S. candidate in Manufacturing Systems Engineering at CSUN
- Bodia Borijin, Intern, B.S. candidate in Structural Engineering at UCSD
- Andrew Wang, Intern, Portola High School
Funding
- Funding Organization: NASA
- Funding Program: MUREP Aerospace High-Volume Manufacturing and Supply Chain Management (MUREP High Volume), Grant number: 80NSSC22M0132
Note: names marked with an asterisk (*) indicate current team