Research Project
In-Space Propellant Tank Venting
(Concept Development and Feasibility Study for In-Space Propellant Tank Venting)
Lead Researchers
- Dr. Vinicius Sauer, Assistant Professor, Mechanical Engineering
- Dr. Bingbing Li, Associate Professor, Manufacturing Systems Engineering
- Dr. Nhut Ho, Mechanical Engineering
Collaborators
- Dr. Matthew E. Taliaferro, Dr. Samuel R. Darr, and Dr. Paul D. Lee at The Aerospace Corporation
Student Team
- Cole Millett, M.S. Mechanical Engineering*
- Alejandro Piscione, B.S. Mechanical Engineering*
- Carl Bejosano
- Nathan Gabriel
- Jesus Sanchez
- Jessica Vasquez
Note: names marked with an asterisk (*) indicate current students
Funding
- Funding Organization: The Aerospace Corporation
SYNOPSIS
To achieve a propellant management system capable of retaining the liquid
propellant while venting ullage, the following approach is being taken:
-
The development of an analytical model to predict the performance of a new type of screen channel liquid acquisition device (LAD).
-
Validating the analytical model by comparing it with existing data and computational fluid dynamic simulations.
-
Collecting experimental data for new screen channel LAD design.
Abstract
Lead Researchers
- Prof. Bingbing Li, Department of Manufacturing Systems Engineering and Management
- Prof. Christoph Schaal, Department of Mechanical Engineering
Collaborators
- NASA JPL: Dr. Douglas Hoffman, Dr. Richard Otis, Dr. Ryan Watkins, Dr. Bryan McEnerney
- NASA Goddard Space Flight Center: Ryan McClelland at Instrument Systems and Technology
- UCLA: Dr. Xiaochun Li, Dr. Morris Wang
- Honeywell Aerospace: Gregory Colvin, Bob DeMers
- Castheon Inc: Dr. Youping Gao, Mr. Steve James
- ASTM Additive Manufacturing Center of Excellence (AM CoE): Mr. Shane Collins
- SimInsights Inc: Mr. Rajesh Jha
- El Camino College: Mr. Jose Anaya
Student Team
- Dr. Changyu Ma, Postdoc in ARCS at CSUN
- Donald Palomino, Fellow, M.S. candidate in Manufacturing Systems Engineering at CSUN
- Paula Logozzo, Fellow, undergraduate student in Mechanical Engineering at CSUN
- Elliot Sadler, Fellow, M.S. candidate in Manufacturing Systems Engineering at CSUN
- Bodia Borijin, Intern, B.S. candidate in Structural Engineering at UCSD
- Andrew Wang, Intern, Portola High School
Funding
- Funding Organization: NASA
- Funding Program: MUREP Aerospace High-Volume Manufacturing and Supply Chain Management (MUREP High Volume), Grant number: 80NSSC22M0132
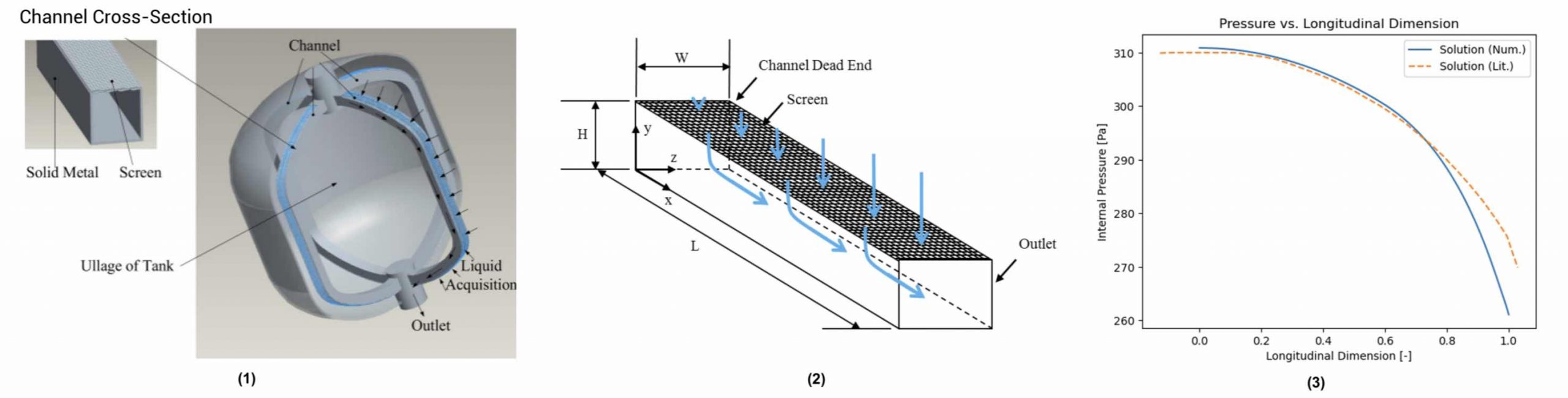
Alignment, Engagement and Contributions to the priorities of NASA’s Mission Directorates
Research Objectives
-
The presence of unwanted vapor, known as ullage, in spacecraft propellant storage tanks proves to be an issue preventing deep space exploration.
-
The presence of vapor propellant leads to over-pressurization of the fuel tanks onboard and less range of travel.
-
The goal of this project is to innovate existing propellant management devices that prevent liquid from being extracted with the ullage.
Research Methods
Enhance propellant management systems’ performance by:
-
Adding converging and diverging effects to channel.
-
Adding varying permeability to the screen via 3D printing
Research Deliverables and Products
-
Image 1 shows a screen channel LAD inside of a typical spacecraft’s fuel tank.
-
Image 2 shows a concentrated view of the screen channel LAD. It is composed of a screened face on the top, 4 solid walls, and an outlet.
-
Image 3 shows the validation of our numerical solution, and the solution provided by literature.
Commercialization Opportunities
-
Application: In-space propellant transfer.
-
Key Values: Enhance liquid propellant retention in spacecraft.
-
Potential Customers: Aerospace industry.
Research Timeline
Start Date: 3/1/2024
End Date: 2/28/2025
Lead Researchers
- Dr. Vinicius Sauer, Assistant Professor, Mechanical Engineering
- Dr. Bingbing Li, Associate Professor, Manufacturing Systems Engineering
- Dr. Nhut Ho, Mechanical Engineering
Collaborators
- Dr. Matthew E. Taliaferro, Dr. Samuel R. Darr, and Dr. Paul D. Lee at The Aerospace Corporation
Student Team
- Cole Millett, M.S. Mechanical Engineering*
- Alejandro Piscione, B.S. Mechanical Engineering*
- Carl Bejosano
- Nathan Gabriel
- Jesus Sanchez
- Jessica Vasquez
Note: names marked with an asterisk (*) indicate current students
Funding
- Funding Organization: The Aerospace Corporation