Digital Twin Integration of openCAESAR and INTREPID to design and additively manufacture the Multiphysics Optical Tracker
Abstract
The project involves multidisciplinary fields including structural engineering, thermal analysis, system engineering, computer programming as well as the application of new developing technology including 3d metal printing fabrication, generative design with Autodesk Fusion360, and Ontological modeling language (OML) with OpenCaesar provided by JPL. One part of the team will setup and create system application of Opencaesar including the ontology. The other part of the team performs the tasks of designing, analyzing, and fabricating of the optical tracker mount case study and utilizes aforementioned Opencaesar application.
Motivation/Research Problem
A major challenge that large organizations or enterprises face is sharing information among different departments or teams. Oftentimes, there are similar or repeat projects that different departments have worked on, but they have come up with their own methods and terminology that make it difficult to follow.
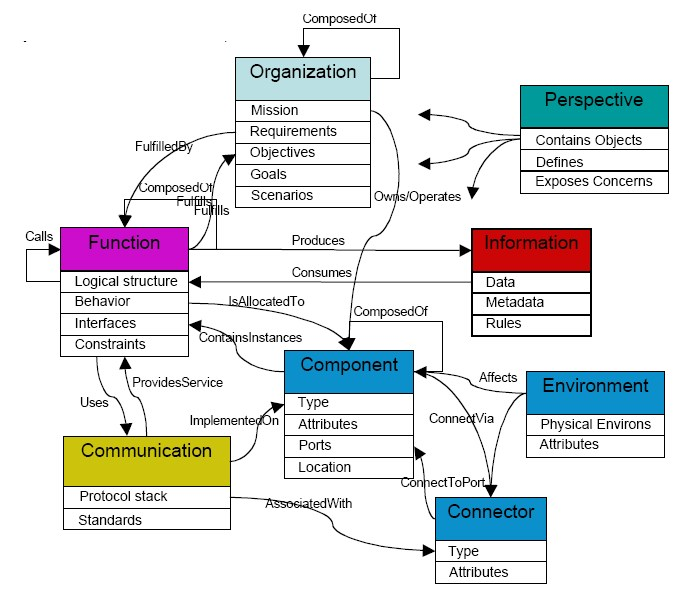
Lead Researchers:
- Bingbing Li, Manufacturing Systems Engineering
- Dr. Nhut Ho, Mechanical Engineering
Collaborators:
- Dr. Maged Elaasar, NASA JPL
- Dr. Richard Otis, NASA JPL
- Dr. Bhupen Lodhia, Autodesk
- Mr. Marco Fiocco, Autodesk
- Mr. Tomas Lay Herrera, Autodesk
- Mr. Akmal Bakar, Autodesk
Student Team:
- Paula Logozzo, Mechanical Engineering
- Max Slade, Anthropology
- Ruitao Wu, Computer Science
- Ting Hsun, Computer Science
- Axel Fernandes, Engineering Management
Funding
- Funding Organization: Autodesk Inc, NASA
- Funding Program: Autodesk Research, MIRO
Alignment, Engagement and Contributions to the priorities of NASA’s Mission Directorates
We will investigate using digital twins in the context of a mission to build small rovers, similar to JPL Open Source Rover (OSR) or NASA’s Cooperative Autonomous Distributed Robotic Exploration (CADRE). The JPL OSR is an open-source, build it yourself, scaled-down version of the 6 wheel rover design that JPL uses to explore the surface of Mars. The OSR is designed almost entirely out of consumer off-the-shelf (COTS) parts. This project is intended to be a teaching and learning experience for those who want to get involved in mechanical engineering, software, electronics, or robotics. NASA’s CADRE project is developing a network of shoe-box-sized mobile robots that could enable future autonomous robotic exploration of the Moon, Mars, and beyond. The CADRE robots are the latest version of NASA’s A-PUFFER technology.
Research Questions and Research Objectives
Our goal is to investigate using digital twins as an agile approach to specify, design, manufacture, integrate and test the mechanical aspects of space systems. This approach allows information to flow between the system development activities, guided by a rigorous methodology that formalizes the relations between them. It also breaks the usual silos between work packages, increases the visibility of work products, maximizes the potential for automation, and minimizes the cost of change.
Research Methods
- Define system requirements models, as well as physics-based design models of key system components, and use them to iteratively specify, build, configure, and test the system with maximum automation.
- Generate an initial grey box CAD model which satisfies system constraints for each design increment.
• Such model will then be augmented with additional design details
• Apply Generative Design optimization analysis to reduce mass while satisfying mechanical load requirements.
• Confirm the resulting model against system requirements and constraints.
• This analysis pipeline will be run automatically whenever a change is proposed and before it is accepted as baseline. Figure 2Grey Box CAD Model & Optimized Model - Additively manufacturing the prototype to save lead time and reduce the costs of molds, fixtures and tools. The 3D printed part will then get integrated into a system prototype that will be available at the end of each iteration.
- Develop the digital twin capability called Integrated System Health Management (ISHM) for additive manufacturing process that can predict defects and generate efficient integration plans.
- Throughout the development process, the digital twin will also generate gate product views for the baseline design (and each change proposal) and make them available to stakeholders for review.
Research Deliverables and Products
One Journal paper and one conference paper
Research Timeline
Start Date: June 2021
End Date: May 2023
Lead Researchers:
- Bingbing Li, Manufacturing Systems Engineering
- Dr. Nhut Ho, Mechanical Engineering
Collaborators:
- Dr. Maged Elaasar, NASA JPL
- Dr. Richard Otis, NASA JPL
- Dr. Bhupen Lodhia, Autodesk
- Mr. Marco Fiocco, Autodesk
- Mr. Tomas Lay Herrera, Autodesk
- Mr. Akmal Bakar, Autodesk
Student Team:
- Paula Logozzo, Mechanical Engineering
- Max Slade, Anthropology
- Ruitao Wu, Computer Science
- Ting Hsun, Computer Science
- Axel Fernandes, Engineering Management
Funding
- Funding Organization: Autodesk Inc, NASA
- Funding Program: Autodesk Research, MIRO