Additively Manufactured Scaffolds for Tissue Engineering
Lead Researchers:
- Bingbing Li, Manufacturing Systems Engineering
Collaborators:
- Hanjun Kim, Assistant Professor, Terasaki Institute For Biomedical Innovation
- Natan Barros, Terasaki Fellow, Terasaki Institute For Biomedical Innovation
- Jonathan A.Kelber, Professor of Biology, California State University, Northridge
- Ali Khademhosseini, Chief Executive Officer, Terasaki Institute For Biomedical Innovation
Student Team:
- Alejandro Gomez, Biology
- Axel Fernandes, Engineering Management
- Runrun Chen, Mechanical Engineering
- Shuyi Huang, Nutrition and Dietetics
- Getaywokal Degef, Biology
Funding
- Funding Organization: NASA, Department of Defense
- Funding Program: MIRO, Defense Manufacturing Community Support Program (DMCSP)
Abstract
Three-dimensional biofabrication is an emerging and promising solution that aims to solve the organ donor shortage problem being faced all over the world. Given that fabricated tissues and organs can be an alternative for replacing damaged human tissues and organs, in efforts to achieve the capability of printing viable tissues and organs, researchers have already begun developing strategies that innovate this idea. Having said that, current biofabrications can be seen as 3D metal-printed scaffolds and 3D bioprinted models. Our scientific team will cover these areas by developing innovative hydrogels that will be composed of biocompatible materials such as gelatin methacryloyl (GelMA) and synthetic nanosilicates. Similarly, a 3D metal-printed model will be constructed using titanium and analyzed for its biocompatibility. By doing so, we anticipate developing an in-vitro MIA PaCa-2 human pancreatic cancer model that would later be used to study a variety of biological principles. We also anticipate that our 3D metal scaffolds will offer a great array for studying various biological disciplines and lead to a greater cause in the realm of biofabrication. From these projects, we aim to publish an ample amount of research work that may contribute to the field of tissue engineering.
Motivation/Research Problem
Fabricated tissues and organs can lead to an alternative for replacement of damaged human tissues and organs. This is an emerging and promising solution that aims to solve the organ donor shortage problem.
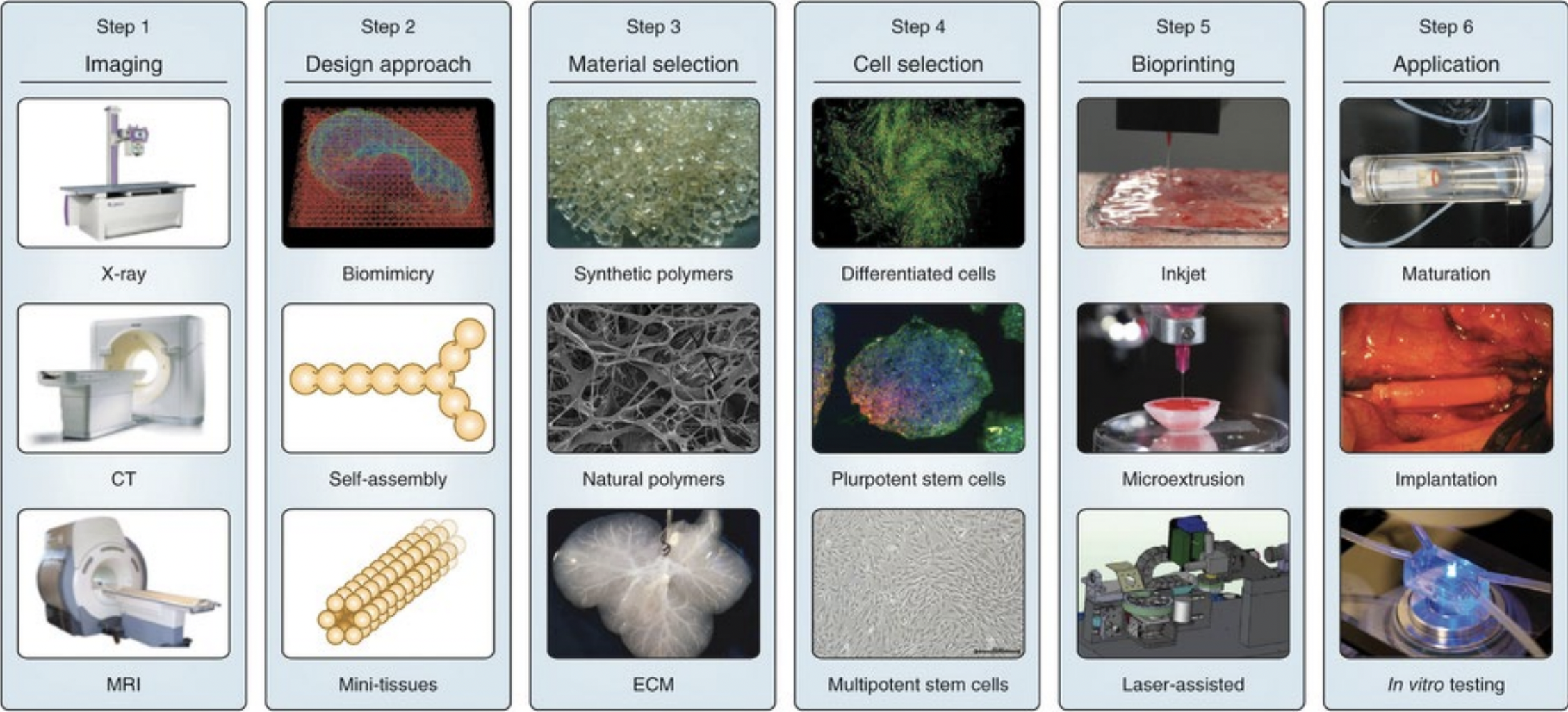
Alignment, Engagement and Contributions to the priorities of NASA’s Mission Directorates
This is the collaborative research with the strategic partner Terasaki Institute for Biomedical Innovation (TIBI). MOU between TIBI and ARCS was signed in October 2021.
Research Questions and Research Objectives
The significance of this project is to:
- Explore the in-vitro and in-vivo study of bone implants through metal 3D printing.
- 3D bioprint MIA PaCa-2 human pancreatic cancer models for innovative research.
Research Methods
- 3D Bioprinting:
- Phase One:
- Innovation of biocompatible biomaterial inks – Record the printability and rheological properties of the established biomaterial inks – Analyze the biocompatibility of the bioinks via the encapsulation of C2C12 mouse myoblast cells.
- Phase Two:
- MIA PaCa-2 and C3H10T1/2, Clone 8 cells were provided by Dr. Jonathan Kelber from the Developmental Oncogene Laboratory at California State University, Northridge (CSUN) – Analyze the biocompatibility of the bioinks via the encapsulation of each respective cell line via metabolic activity. – Analyze the biocompatibility of the bioinks via the encapsulation of Co-Cultured MIA PaCa-2 and C3H10T1/2 cells.
- Phase Three:
- Utilize microscopy to visualize the following: LIVE/DEAD, F-actin, and nuclei – Additionally, use microscopy to visualize markers such as α-SMA and CK – Preform biological technique such as ELISA and Real Time QPCR to quantify the expression of proteases and cytokines – Analyze our data, and draft the manuscript of our findings for publication 3D Metal Printed Implants
- Phase One:
- 3D metal printed implants:
- Phase One:
- Development of titanium scaffolds (CAD Design) – Manufacturing of cylindrical titanium scaffolds with various pore sizes utilizing Renishaw AM400 laser powder bed fusion system – Using SEM microscopy, visualize the surface area of the manufactured cylindrical titanium scaffolds.
- Phase Two:
- Test hydrogel crosslink ability within the sample using UV light – Compare cell viability between samples with No hydrogel versus samples with cross linked hydrogel via metabolic activity analysis. – Determined the cell line required to carry on the project into the future experiments (both in-vitro and in-vivo animal studies)
- Phase Three:
- TBD
- Phase One:
Research Deliverables and Products
- Products (anticipation):
- Innovation of a biocompatible bioink/embedded printing support bath
- Development of an in-vitro MIA Paca-2 pancreatic cancer model
- Development of bone implants, and analyze of biological disciplines
- Publications:
- Aim to publish research work on both aspects of this project
Research Timeline
Start Date: October 2019
End Date: May 2023 (3D Bioprinting: Tentative Publication); Indefinite (3D Metal Printed Implants)
Lead Researchers:
- Bingbing Li, Manufacturing Systems Engineering
Collaborators:
- Hanjun Kim, Assistant Professor, Terasaki Institute For Biomedical Innovation
- Natan Barros, Terasaki Fellow, Terasaki Institute For Biomedical Innovation
- Jonathan A.Kelber, Professor of Biology, California State University, Northridge
- Ali Khademhosseini, Chief Executive Officer, Terasaki Institute For Biomedical Innovation
Student Team:
- Alejandro Gomez, Biology
- Axel Fernandes, Engineering Management
- Runrun Chen, Mechanical Engineering
- Shuyi Huang, Nutrition and Dietetics
- Getaywokal Degef, Biology
Funding
- Funding Organization: NASA, Department of Defense
- Funding Program: MIRO, Defense Manufacturing Community Support Program (DMCSP)